ARTICLE SUMMARY
Why do Lean initiatives go wrong? For all possible reasons, but the root cause is usually one and it is ridiculously obvious.
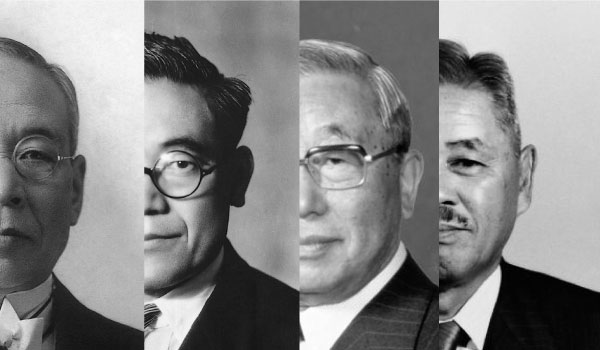
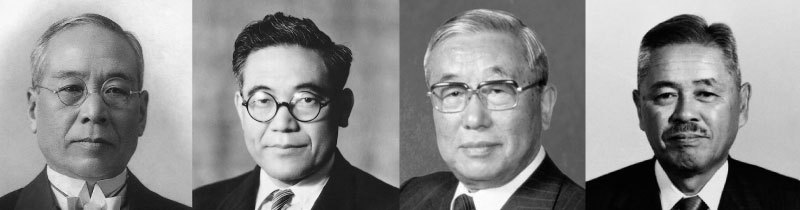
Why do Lean initiatives go wrong? For all possible reasons, but the root cause is usually one and it is ridiculously obvious.
Once, we believed it was because Lean could only work with Japanese people. The Toyota Production System was born inside Japan, so it can only be our non-Japanese father and mother’s fault. Another excuse was that Toyota makes cars, so the Toyota Production System could only work with car manufacturing.
If not, the answer was a fusion of the two: we’re not Japanese and we don’t make cars! In fact, the answer to this question today is pretty clear and it was discovered a few decades ago. It’s the same answer for any kind of organizational change: the human being and leadership.
When you see that beautiful board in your boss’s office with the company’s mission, vision and values, you’re not really looking at the company’s mission, vision and values. This does not exist. Walls, machines, chairs and offices do not think, they have no will and cannot write. Therefore, they can’t open a business. Consider this:
- There’s no company mission: there are the problems that the CEO dreams of solving in hopes to make money by constantly solving the problems in question.
- There’s no company vision: there’s the path that the CEO wants to follow to solve problems and make money by following it.
- There are no company values: there are the values that the CEO has (or that pretend to have) because the market would value the product more if they showed these values.
Everything that happens, and the culture that forms within a company, is the result of how this person thinks and what they know. The way they think and what they know dictates their behaviors and values, and consequently encourages the behavior of others, as the CEO has the power of decision.
Sakiichi Toyoda (first in the cover photo of the post) took off the mindset of Kiichiro Toyoda (the second), his son and founder of Toyota Motor Corporation. This way of thinking was critical for Taiichi Ohno (the last of the post’s cover photo) to make Lean happen, supported by Kiichiro and Eiji Toyoda (the third in the photo), who would become one of the company’s future presidents.
As for the rest of the world’s leaders, who are not part of the Toyoda family and haven’t worked for decades at Toyota, they need to understand two super special factors or they won’t be able to handle a Lean initiative. These two factors answer not only why Lean initiatives go wrong, but also because even knowing the answer, they keep going wrong for some people.
Let’s check out both!
1. We’re human beings! Many leaders don’t know how to handle it.
It’s human nature that any Lean initiative could go wrong. Or less specifically: it’s human nature that any change could go wrong. What is a company if not a group of human beings doing something for the world and for themselves simultaneously?
The problem with doing something is that we’re creatures of habit, with an extremely powerful machine called a brain that best learns new habits by repetition. To think and to practice Lean is not the traditional habit for most people (Henry Ford taught other behaviors, and they have become the standard business set), so we have the main ingredient for Lean initiatives go wrong.
While this machine loves new things, it hates the process of change required to turn this newness into a habit. That’s because the brain naturally saves energy due to its cognitive limitation (our tool for understanding and interacting with the world).
Turning a new behavior into a habit (that is, by doing so much, learning and memorizing the required connections to then being able to “outsource” the service to the subconscious) is the way the brain saves energy. For example, this allows you to breathe without having to keep remembering to breathe all the time.
But creating a new habit means getting out of that coveted comfort zone, ordering the brain to perform things it doesn’t know how to do well yet and this action consumes tremendous energy.
That’s why the brain keeps you from making huge efforts in Lean initiatives, as it’s trying to convince you to go back to the previous state, where things were familiar and you had the answers to what, how and when. Ironically and tragically, most leaders don’t know this. Consequently, if leaders don’t know how to handle it, they will not know how to deal with people in general.
2. They don’t know what Lean really is about
Lean is a work philosophy? A method to increase profits? A set of tools to boost productivity? Philosophy, methods and tools: they are all part of what Lean is, but none of them in isolation make a Lean initiative work. Especially methods and tools that usually catch the attention of beginners.
Nowadays, the excuse for lack of knowledge doesn’t make sense anymore. Can’t afford a sensei’s consulting? Go after the books, visit the internet.
The Toyota Production System (STP) and its results were presented to the world by a book called The Machine That Changed the World nearly 30 years ago. Since then, all the nuances of the Toyota Production System and Toyota’s internal culture have been and are being studied daily, giving rise to a dozen more spectacular books.
As much as some terms change, we have known for decades what the essence of Lean is, so what is missing is a desire to learn.
Is there any salvation for Lean initiatives?
Yes. In fact, it has always been: letting natural selection do what it has always done, not only in general life, but also in the business world. After all, Lean is nothing more than the result of Toyota’s natural attempt to survive the struggles of its time, which, as reality proves today, turned out to be the best way to survive the future.