ARTICLE SUMMARY
Among the possible steps to begin a Lean transformation, one of the most famous (and beloved) is the Kaizen Event. Kaizen Events are usually meetings of one week (completely dedicated to the whole week), where a cross-functional group and a facilitator come together to develop a solution for organizational problems. However, like we often see in life, despite bringing results with phenomenal speed, this type of action also has its flaws.
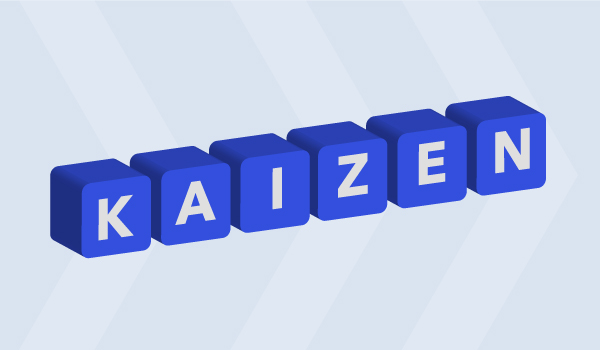
Among the possible steps to begin a Lean transformation, one of the most famous (and beloved) is the Kaizen Event. Kaizen Events are usually meetings of one week (completely dedicated to the whole week), where a cross-functional group and a facilitator come together to develop a solution for organizational problems. However, like we often see in life, despite bringing results with phenomenal speed, this type of action also has its flaws.
Controversies and Traps
Few people will tell you this (maybe no one), but Jim Womack, one of the greatest scholars of Lean in the world, mockingly named Kaizen Events as kamikaze-kaizen events.
His intention was that you should quickly and ferociously address problems. The important thing is that Kaizen Events are not bad but some companies end up transforming all of their Lean initiatives into Kaizen Events, even counting them as some kind of KPI. So, let’s begin this article with the mistakes of this approach:
- Kaizen Events are unique episodes that happen in a specific part of the processes, regardless of the processes flow as a whole;
- At the end of a Kaizen Event, we usually have an enormous to-do list which will not be taken seriously most of the times;
- Despite the fact that everyone will get excited during the workshop, when it’s over the reality is quite different and the results get lost over time;
- There’s a tendency to analyze Kaizen Events based on short-term financial returns, cutting the possibility of lasting change;
- It does not bring lasting cultural changes.
Great Benefits You’ll Find
Take it easy, not everything is lost and each company that defines itself as going through a Lean journey should take this seriously and hold at least one Kaizen Event. Check it out the bright side of this initiative:
- It’s a terrific experience for the involved participants. The feeling of problem-solving driven actions plus the team spirit has a great power to unfold the visions of people, allowing for the possibility of recognizing waste before and after it happens;
- The management team can see that fast results can be achieved with the right amount of focus, dedication and resources;
- The feeling of experiencing a Kaizen Event provides high impact learning. People can learn things that would be impossible in a traditional classroom approach;
- Resources for change (material and intellectual) are available without traditional bureaucracy;
- In a traditional classroom, people that don’t believe in changes would find numerous reasons to contest Lean, while at a Kaizen event, they are not only seeing the change, but also making it happen in practice;
- You can use Kaizen Events to implement some aspects into the Value Stream.
Making your own Kaizen Event
Now that you’re all excited about changes, but also aware of what doesn’t matter, it’s time to get your hands dirty. To do so, we’ll follow the recommendations of the sensei Jeffrey K. Liker and David Meier!
Step 1: Preparation of the event
Two to four weeks before the Kaizen Event you’ll need to:
- Define the scope of the problem to be solved (solving a problem that did not exist before is worse than not solving any problem);
- Choose the team (someone must have decision-making power and those involved in the area/activity where the problem happens must be present);
- Gather data on the problem and the current situation;
- Decide which Lean techniques will be needed;
- Make logistical adjustments for the Kaizen event;
- In some cases, purchase the required materials and equipment when the lead time is longer than the duration of the event.
Step 2: The event itself
The time has come and our sensei has a calendar suggestion following the PDCA, so you can move on to success in your Kaizen Event:
- Monday: give the team an overview of what Lean is and teach them any tools and techniques they need. After this, begin the data gathering of the process;
- Tuesday: this is the Plan phase. Finish analyzing the current state of the problem, collect info, draw the process map, draw the flow patterns within the area layout and establish Standard Worksheets and Standard Work Combination Tables, etc. Only then you can begin to think about the improvements for the future;
- Wednesday: The Do phase. It can be done in the form of a test pilot or by moving straight to final implementation;
- Thursday: Check and Act time. Evaluate the results and make the necessary corrections until the result is satisfactory;
- Friday: report the results to your leaders and celebrate with your team!
Step 3: Follow up
Not all improvement items can be completed in a week, so we need to create a to-do list with a 5W2H action plan and follow up closely so that nothing is left behind.
Ready to begin the changes? Have you ever joined any Kaizen Events? Tell us on LinkedIn!
Bye and have a good Kaizen!