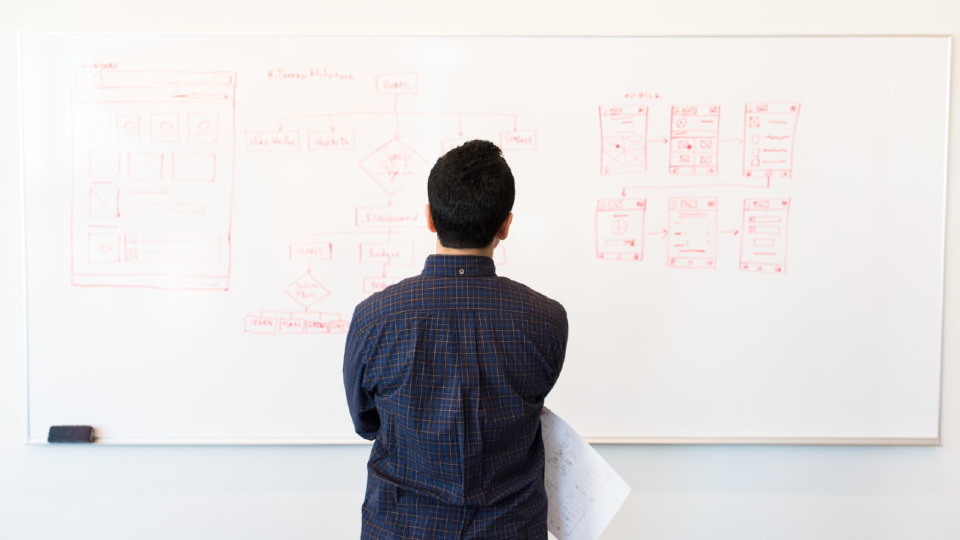
Last reviewed and updated by Team Pipefy on .
In our fast-paced world, companies are constantly tracking and improving their processes and workflows to stay one step ahead of the competition. Continuously monitoring the performance of processes and workflows is necessary to identify and resolve potential bottlenecks and issues before they can balloon into more significant problems.
In this blog, we’ll cover what continuous process improvement (CPI) is, the purpose of CPI, the benefits CPI provides, and various procedures used for implementing CPI best practices in your organization.
See how no-code automation helps business teams and IT No-code Automation: Good for Business, Great for IT
What is continuous process improvement (CPI)?
Continuous process improvement is a strategy or methodology businesses and organizations can implement to monitor their business processes and make incremental upgrades to increase quality and efficiency.
We often underestimate the impact small changes have and overestimate the impact of implementing a large change. CPI is the act of making small tweaks to business processes and procedures with the knowledge that each minor improvement adds up to exponential changes over time.
Operational excellence can only be achieved with continuous changes that aim to boost effectiveness, increase output quality, improve flexibility, and make all types of business processes as efficient as they can be over time.
What is the purpose of CPI?
The primary purpose of CPI is to establish a standardized and consistent process for improving the workflows and processes within an enterprise. If a company doesn’t create a definitive plan for improving its processes, it’ll likely find itself slowly regressing instead of improving.
Big changes can often be overwhelming and tedious to implement, but small changes usually have much smaller barriers to overcome. CPI is a way to improve your company’s processes and leverage the power of small changes to take your organization up to its maximum potential.
For continuous process improvement to work and make the task feel less overwhelming, establish a CPI process and assign specific team members as “owners” of each step so that small changes can be made consistently and continuously over time.
Benefits of continuous process improvement
The primary benefit of continuous process improvement is its ability to effectively identify inefficiencies and remove bottlenecks in your company’s processes over time. CPI is the perfect practice for streamlining workflows and optimizing your business without overwhelming everyone with massive changes.
Here are some of the primary benefits of CPI and how they can make a significant impact on your business:
Error reduction
When trying to implement massive changes, there’s a high probability of delays and errors happening throughout the process. With CPI, minor changes over time ensure that fewer errors have the chance to crop up.
Lower costs
CPI can significantly reduce costs for your company by identifying bottlenecks and inefficiencies in your current processes. For instance, if your company currently has a legacy workflow or system that’s time-consuming, hard to manage, and resulting in high costs, a continuous process improvement process can identify the root of this excess cost, create a plan to improve or streamline such systems, and allow your organization to save a significant amount of time and money.
Improved productivity
Process and workflow bottlenecks can reduce outputs and lower productivity within your organization. With CPI, you can identify these problems, like ineffective transfers of work or communication, and eliminate them in small waves until outputs and productivity increase.
Enhanced customer service
Your customers and clients are the lifeblood of your business, and ensuring their happiness should be a primary priority. By using CPI, you can streamline your customer service processes to improve response times, create better customer experiences (for existing and potential customers), and increase customer retention.
Methodologies used for CPI
Continuous process improvement (CPI) can be implemented using a number of different methodologies. We’re going to cover several methods you can use to implement CPI in your organization.
Kaizen
Kaizen is a rapid improvement process that’s viewed as one of the “core” lean production methods. It is used by companies or enterprises for eliminating waste, improving workflows and processes, achieving continuous process improvement, and seeing exponential growth in efficiency and effectiveness over time.
Using the Kaizen method includes:
- Setting goals and objectives, and identifying any background information required for successful implementation.
- Reviewing the current state of processes and workflows and developing an improvement plan.
- Implementing the improvements identified.
- Reviewing how those improvements perform and fixing what doesn’t work.
- Reporting results and determining how follow-up will be conducted for future improvements.
5S
5S is a lean CPI strategy that’s used to optimize productivity and reduce waste for an enterprise or organization. It originates from five Japanese terms that are used to create a suitable workplace capable of lean production and visual control.
The 5S method can be used to efficiently set up workflows and processes for CPI due to its focus on standardization. This is an excellent method for optimizing productivity throughout a continuous process improvement workflow.
The 5S strategy consists of:
- 整理 Seiri (sort). Separate necessary tools, parts, and instructions from unnecessary ones, and remove the ones that aren’t needed or that are wasteful. This can be applied to CPI by mapping a process that needs improvement and identifying areas that are wasteful or inefficient.
- 整頓 Seiton (set in order, or straighten). Neatly organize and identify tools and parts for easy use. For CPI, this is a chance to assess and organize resources (like people) or tools (like process management software) to be best utilized.
- 清掃 Seisou (shine). Execute a cleanup campaign. In a process improvement workflow, this can mean encouraging and empowering teams to identify and suggest improvements they think may benefit processes and the company as a whole.
- 清潔 Seiketsu (standardize). Perform Seiri, Seiton, and Seiso (the previous three points) on a daily basis to keep your workplace organized and in peak condition. Regularly reviewing processes and making improvements is a key step in CPI.
- 躾 Shitsuke (maintain). Make following the first four S’s a habit.
Value stream mapping (VSM)
VSM is a visual method of continuous process improvement that takes a holistic view of an entire system’s current state to design the future state. Value stream mapping outlines existing workflows and processes and identifies inefficiencies or waste.
Whether the value stream map is hand-drawn or designed using process mapping software, the purpose of a VSM diagram is to show both material and information flow through a process, like how long various tasks take to complete and how often orders are placed from suppliers.
The primary elements of a value stream map include:
- Information flow. Define what information moves through your business processes. This can be order data transmitted to your supplier, production control information, and customer information.
- Material flow. Identify what materials move through your supply chain and what processes they flow into.
- Lead time. Once you’ve mapped out information flow and material flow, map lead times to the appropriate steps of your processes to measure how long a process takes to complete.
- Process time. Similarly, apply processing times to workflow items. This can include information like the amount of time it takes to transport a completed product from a factory to a warehouse.
PDCA cycle
The PDCA cycle is another method for making continuous improvements to your company’s workflows and processes. This cycle has four primary steps:
- Plan. Brainstorm the inefficiencies you currently see and want to start with. Make a plan to tackle them one by one.
- Do. Execute and implement small adjustments for the inefficiencies you located.
- Check. Let your process run and monitor how your adjustments are performing.
- Act. If your improvements are working well, scale up and implement those changes on a larger level.
To continue the CPI cycle, repeat these steps as additional inefficiencies are identified.
Build better workflows and processes for any team The IT Guide to Workflow Management
Steps to create a continuous improvement cycle
- Map process and identify issues
- Plan process improvements
- Implement changes
- Review performance of improvements and repeat
1. Map process and identify issues
The first step of the CPI cycle is to map out all of your current processes and workflows and identify any issues you currently have. What problems or bottlenecks are you currently seeing or facing? Is there anything your team members or employees are commonly pointing out or complaining about?
If mapping all your processes is too overwhelming, start with a single, high-priority process.
2. Plan process improvements
Once you’ve mapped your trouble processes and identified the issues you want to address, the next step is to create a plan for process improvements.
In addition to outlining improvements, it’s important to also consider internal resources, availability, and timelines throughout your planning to successfully implement changes.
3. Implement changes
Once all of your process improvements have been identified and you have an implementation plan, it is finally time to make those changes and implement them into your workflows and processes. Take the time to implement each fix carefully, and communicate changes with your team.
4. Review performance of improvements and repeat
After implementation, your organization needs to monitor the processes or workflows you changed and compare them to how they performed before any changes were made. Are your processes performing better? Are they more streamlined? Are your costs higher or lower?
If you notice positive improvements, it is time to resolve to the next issue. If the results are negative, it’s back to the drawing board and planning out alternative solutions for the issue you’re trying to solve.
Continuous process improvement examples
Various industries can benefit from continuous process improvement. While this is not an exhaustive list, here are some CPI examples and how they can be applied.
Time audits
Manufacturers are constantly trying to improve their processes and increase efficiency and output while reducing costs simultaneously. Performing time audits can help measure inefficiencies and uncover the reason behind manufacturing slowdowns.
Here’s how a manufacturer might implement CPI for solving time inefficiencies:
- Identify any bottlenecks in production times that are affecting a particular production area. Your manufacturer may notice a time inefficiency where parts take longer to complete than usual.
- Brainstorm about what could be causing the inefficiency and inspect the area to narrow down the cause. Make a plan for fixing the inefficiency based on what is observed.
- Implement the plan that was created. If your solution involves clarifying the steps workers follow, this could mean developing clear guidelines and processes for workers in the production area to follow, as well as training them on these new workflows.
- Once the changes have been implemented, monitor that production area for several weeks and take note of whether the actions you’ve taken solved the time inefficiency, or if it still remains. If the time inefficiency has not been resolved, go back to the first step and repeat the CPI process once again.
Surveys
Software sales teams are often competitive and compensated based on how many sales they can bring in. The sales process can be analyzed and run through CPI in order to ensure that productivity and results are consistently improving.
A sales team might implement CPI by gathering process feedback from the individuals who handle and work within the sales process (like prospects or customers) and identifying areas of improvement. This is how a software sales team can implement CPI by gathering process feedback:
- Survey team members who work with the sales process on a daily basis and ask them what can be improved.
- Based on problem areas that are identified, brainstorm possible solutions to each problem and create a plan for implementing changes that could solve each issue individually. Make this plan as detailed as possible to increase the probability of success.
- Implement the plan that was created. If a team member suggested that their sales team should meet once a week to discuss quotas and talk through common issues they faced that week, schedule a meeting time.
- Monitor changes after they’ve been implemented by surveying members of the sales team a few weeks down the line. Have the changes been beneficial or detrimental? Depending on the outcome, if improvement is still required then you’ll have to go back to the first step to repeat the CPI process once again.
How continuous process improvement integrates with broader business strategies
Continuous process improvement (CPI) is most effective when it’s not treated as a stand-alone initiative. The most successful organizations weave CPI into the fabric of their broader business strategies, using it to drive progress in areas such as digital transformation, compliance, customer experience, and operational scalability.
In today’s fast-changing markets, agility has become a core business capability. CPI supports this agility by enabling organizations to adapt quickly, improve resilience, and continuously fine-tune processes in response to evolving needs. According to McKinsey (2024), companies that maintain a consistent process improvement cadence respond to market and regulatory changes 30% faster than peers.
Here are a few key ways CPI aligns with broader strategic priorities:
- Digital transformation: Streamlining and improving processes is a natural first step in any digital initiative. Automating a broken process only amplifies inefficiencies. CPI ensures that workflows are optimized first, so automation efforts deliver real gains.
- Compliance and risk management: In regulated industries, CPI supports better governance by creating more transparent, traceable processes. This helps organizations maintain audit readiness and reduces exposure to operational risks.
- Customer experience: Process efficiency directly influences the quality of customer interactions. Improvements to areas like onboarding, support, and service delivery translate into better experiences, stronger retention, and improved customer satisfaction scores.
- Operational scalability: As organizations grow, well-optimized and standardized processes are critical for scaling efficiently without adding complexity or cost. CPI helps teams continuously refine operations so they can grow in a sustainable way.
CPI also plays an important role in shaping organizational culture. When leaders foster a mindset of continuous improvement across teams, they encourage experimentation, ownership, and collaboration — all qualities that contribute to long-term success.
The right tools make it easier to embed CPI into the company’s strategic roadmap. Platforms like Pipefy help connect process improvements with broader business goals by giving teams visibility into performance, supporting cross-functional collaboration, and providing actionable insights for future optimizations.
Improve your processes with Pipefy
Manually managing continuous process improvement initiatives can become time-consuming and may lead to additional delays or errors, resulting in yet another process management issue to resolve. But with the right tool, teams can easily standardize process improvements and more.
Pipefy is a no-code automation solution that simplifies continuous process improvement. Its visual user interface means that no coding knowledge is required to build processes or improve workflows, making it easy to streamline communication, reduce errors, and eliminate time-consuming tasks with automations.
With an IT-approved toolbox that includes features like forms and real-time process analytics, you’ll be able to gather feedback from teams, measure the performance of process improvements, and identify additional areas of improvement with ease.