ARTICLE SUMMARY
Kaizen is the soul of Lean which is a dynamic set of practices born in Japan inside Toyota, also popularized as The Toyota Way. Find out more about it here.
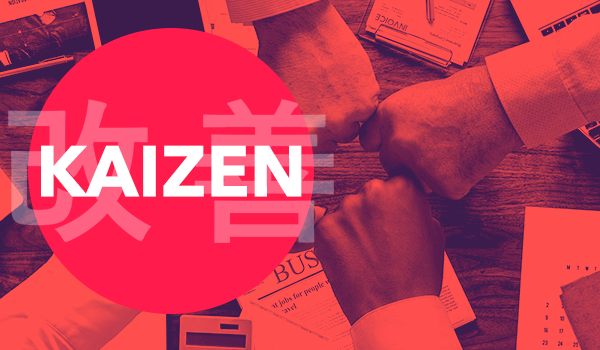
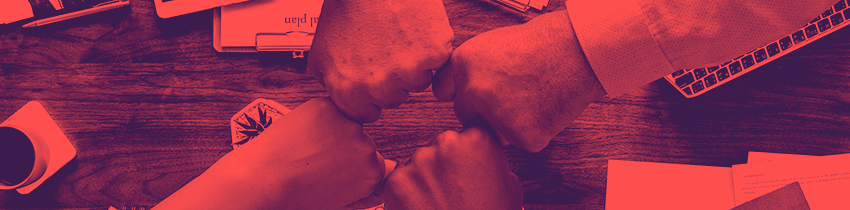
The journey for professional growth is one of the key ingredients for success. Who doesn’t want to become a better professional (regardless of position or field), develop new skills and impact their surrounding environment with positive changes? This pathway is not led only by studying and working, but by having a strong mindset of continuous improvement (or Kaizen).
Not coincidentally, Kaizen is the soul of Lean. Lean is a dynamic set of practices born in Japan inside the Toyota Production System (TPS), also popularized as The Toyota Way, which is directly connected to Kaizen. If you want to explore what Lean is before jumping into Kaizen definitions, consider reading our Guide for Future Lean Experts.
Kaizen is a Janapense word that can be translated as a change for the better (or continuous improvement). It’s a simple yet pivotal concept that should always be on your radar.
Subscribe to learn more about Lean:
The goal is not only to humanize the workplace but also to eliminate wastes and empower people to conduct their tasks in a much better way through concepts and techniques we will later explain. Kaizen improvements bring great results over time, encouraging workers in all positions to experiment and try out new ideas–there’s no place for ordinary results.
Kaizen Everyday, For Everybody, Everywhere
Although Kaizen can be applied in different areas of life, we’ll be focusing on the professional field, but keep in mind that these concepts can be used in several contexts. If Kaizen doesn’t walk together with Lean tools, practices and principles, it’s only half-baked. Remember this:
So, let’s take a look at the Kaizen Principles:
- Respect for people.
- Improvement never stops.
- Elimination of old practices.
- Proactivity to solve problems.
- Creativity to find low-cost gains.
- Empowerment of employees to speak up.
- Gathering of opinions from multiple people.
- Application of solutions as you find mistakes.
These principles may change a bit from one source to another, but in essence, we have 8 pillars that should be intrinsic in any company, team or even a professional that wants to follow a Kaizen philosophy. To help you keep track of your actions, it’s possible to follow this chart:
Check out some of the main tools and principles of Lean management that will help you with:
- Value Stream Mapping: A flow visualization of all steps required to deliver a product or service. It’s the design of the current state and the future state to be achieved.
- Pull System: A flow planning system that takes demand into account to begin the production only when needed (therefore avoiding waste).
- Five Whys: The Five Whys technique consists of questioning yourself or your team five times or more of why a problem or defect happens until you reach the root cause.
- Kanban: A type of flow designed by columns and cards in which everyone can follow the progress of the processes, know who is doing what and what still has to be done.
- Yokoten: It can be translated as horizontal deployment and it’s all about sharing good results and examples of Kaizen from one area of a company to another.
- PDCA: Plan, Do, Check and Act. A four-step management method used to control and improve processes and products of any kind.
- 3 Ms: The 3 Ms stands for Muda, Mura, and Muri. They represent waste, overburden and unevenness, respectively. In order to achieve better flow, the 3 M’s must be neutralized.
- 5 Ss: Sort, Set In Order, Shine, Standardize and Sustain. The 5 Ss create and maintain an intuitive workspace. It’s all about a great environment for the employees.
Through these actions, you will obtain better processes and a clear flow of your tasks. Keep in mind that Kaizen has to be in your daily routine in order to be effective, whether within the whole company, a specific team or in one person’s work. It’s not something to take on once, but regularly.
Kaizen Event: When Actions Take Place
In order to have a kick-off for practical actions of continuous improvement, it’s possible to host a Kaizen Event, which is nothing more than a gathering of people involved in the processes to be perfected. Although Kaizen has a more cultural aspect inherent to it, the Kaizen Event is where everyone actively participates in the ongoing changes.
But in which scenarios should you consider hosting a Kaizen Event?
- When an immediate boost is needed.
- When the matter requires collaboration among employees.
- When the problem is greatly interfering with business processes.
- When the issue can be solved through actions of a Kaizen Event.
- When team members need to learn rapid improvement techniques.
Kaizen Events have a number of different names (Kaizen Blitz, Kaizen Burst, Kaizen Circles and so on), but traditional ones usually last for a week. Of course, nothing is set in stone, it depends on your context and the issue to be resolved. In a conventional Kaizen Event you will find:
- Team Leader: The facilitator of the event. Responsible for managing the event activities, the proper use of tools and focusing on the objective.
- Process Owner: Responsible for the event itself, in charge of scheduling the place where the event will happen and all the structure for its success.
- Senior Manager: The professional involved in the early planning of the event. Works directly with the Team Leader, but is not so active when the event is taking place.
- Kaizen Coach: The expert that makes sure principles, practices and tools are being correctly applied. Therefore, it must be someone with a deep knowledge of Kaizen.
- Team Members: Last but not least, the actual team members included in the process of improvement. This number can drastically change depending on the size of the event.
Once all positions have been appointed, it’s time to put the event into action! Remember that the event doesn’t have to strictly follow all mentioned rules, you can adapt it seamlessly. Also, you will want to retain 100 percent focus as long as the employees are pulled away from their normal day-to-day tasks. Planning is essential so that work routines aren’t affected.
An interesting way to get into the skin of anyone involved in problematic or inefficient processes is to follow the 3G guideline. No, we’re not talking about the old 3G phone signal, but rather, the 3G Principles: Gemba, Gembutsu and Genjitsu. Check out what they stand for:
- Gemba: The place where the work happens. The idea here is to walk around and talk to all involved in the processes in order to better understand the problems to be erased.
- Gembutsu: The product or process itself to be improved. It’s critical to have a clear view of where value is created in order to prioritize it and remove possible wastes.
- Genjitsu: The facts. You have to identify and deal with the root causes that led the situation to its ineffective state. Only then you can avoid them in the future.
When applying a Kaizen Event, you must have a selective eye for specific things. Sometimes, the solution is not far out of eyesight, but since we’re used to the way things work we may not find easy alternatives for improvement–that’s why the participation of the whole team is so relevant. Cooperation is one of the mottos of a Kaizen Event.
The actual activities that take place within any Kaizen Event can differ a bit from one to another, but practically all of them use the tools and concepts that we presented previously: 5 Whys, 5 Ss, Value Stream Mapping, Kanban, Pull System, PDCA and so on. The following script should always be taken into account:
- The current state of the process is mapped and documented.
- All potential improvements are listed and considered.
- The chosen improvements are deployed and tested.
- All results are evaluated and documented.
- Avoid falling back to old habits.
The Kaizen Event must be an enthusiastic problem-solving moment in which all employees feel free and comfortable enough to suggest improvements, without judgments. Keep in mind that the follow-up of the event is as important as the event itself since metrics and KPIs are tracked. Not only the processes but the trust of the group, will be evaluated after the event.
Remember that Kaizen and Lean always walk together. One way to reap the benefits of this match is to use a tool for processes management that connects both of them. Pipefy is the Lean management platform that enables the Kaizen culture by bringing teams together in streamlined processes.
Ultimately, Kaizen is a philosophy, a mindset and an attitude of problem-solving. In the end, it’s all about personal and professional continuous improvement to achieve outstanding growth.