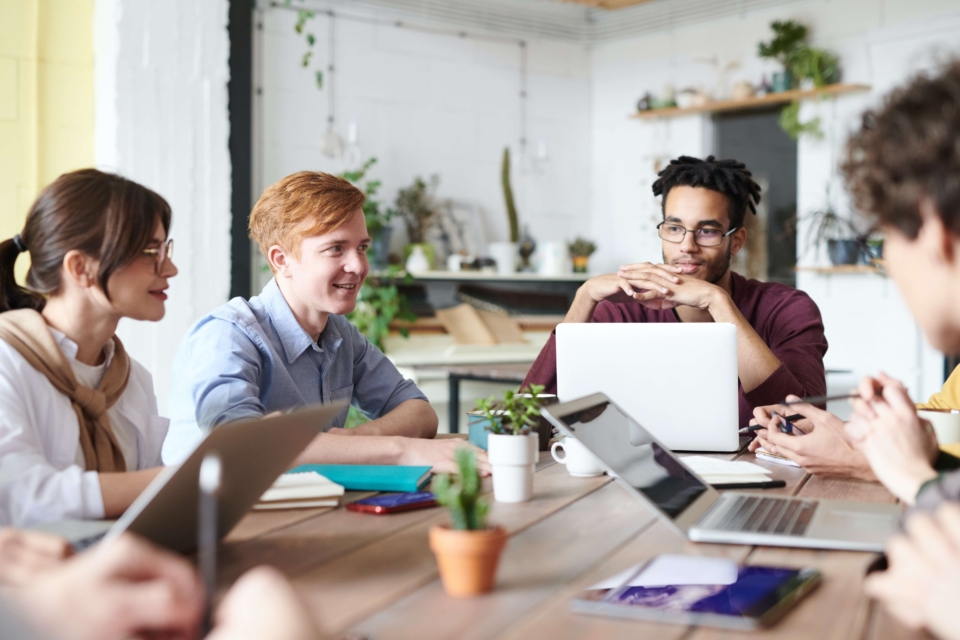
The lean management model uses five core principles to pursue a philosophy of continuous improvement. It has proven to be highly effective in team management, particularly in industries such as construction, manufacturing, and software development.
The holistic approach of lean management provides positive results over the long term, but it requires a culture that welcomes change. This guide discusses the principles of lean management in addition to its benefits and best practices for implementing it.
Definitive Guide to Business Process AutomationGet started
What is a lean methodology?
Toyota Motor Corporation in Japan originated the lean methodology for manufacturing. It’s a systematic approach to eliminating process waste, allowing companies to deliver greater value to customers while using fewer resources.
These methodologies accomplish this goal through means such as engaging employees, minimizing inventory, optimizing workflow, and reducing lead times. Lean methodologies have since been applied to many industries outside of manufacturing, including healthcare and software development.
What is the difference between the various lean methodologies?
Terms like lean manufacturing, lean engineering, and lean management refer to the application of lean principles within a particular industry. Lean agile is the combination of lean and agile methodologies, which share many similar values.
The Lean Six Sigma principles comprise a type of lean methodology that focuses on defect prevention, usually in manufacturing.
The 5 lean principles
The five principles of lean management include:
- Identifying value,
- Mapping how value is created,
- Creating a flow,
- Establishing a pull system, and
- Always seeking improvement.
1. Identify value
Implementing a lean process requires you to first identify the value of the team’s work. This step primarily consists of distinguishing between activities that add value to the process and those that don’t. All team members must actively participate in this activity to ensure it remains aligned with all requirements.
In the context of lean management, value is what users get from the end product. Users are typically the company’s customers, but they can also include other members of the organization.
Assigning value also involves categorizing waste activities, which don’t directly contribute towards an item’s value. Lean recognizes that some waste activities support activities that add value, while others only harm the workflow.
Quality Assurance, or QA, is a common example of necessary waste. It doesn’t create direct value for the customer but does support the development of value, which is what makes it necessary.
2. Map the value stream
Mapping the value stream allows team members to visualize the path that value takes to reach customers. Lean management typically uses Kanban boards to perform this step, which Toyota originally developed for its production system.
A basic Kanban board consists of a flat, vertical surface with three columns or phases labeled Requested, In Progress, and Done, indicating the three primary states for an assignment.
You can map progress in greater detail by breaking these phases into smaller steps. For example, the Requested phase may include steps like Order Received and Ready to Start.
Some industries like software development have a particularly large number of steps in each assignment category.
3. Create flow
Flow is a key concept in lean management that refers to the flow of value to the customers. The goal of this step is to ensure the smooth delivery of value, which is often impeded by process bottlenecks.
Managers must keep a close eye on bottlenecks, which often requires them to dig deeply to figure out why it’s happening. Common causes of bottlenecks include waiting for actions to be completed by external stakeholders, like approvals, or a lack of capacity or resources at a particular stage.
In some cases, completely eliminating a bottleneck may not seem possible, so achieving partial alleviation — such as streamlining steps, limiting requests, or extending work turnaround times — is a more realistic goal. The key here is to implement changes that improve the flow.
For example, a review phase is a common source of bottlenecks since the number of people submitting work items is usually far greater than the number of people reviewing them.
A simple solution to this issue is to place a limit on the number of work items that can be open at any time. Setting a work-in-progress, or WIP, limit requires a discussion with both the development team and the employees performing the tasks to determine the limit that will maximize efficiency.
4. Establish pull
A pull system is one in which a team only starts work when there’s a need for it and the team has the needed capacity. The goal of this step is to create value when the customer needs it to avoid producing a surplus.
Tasks that need to be performed are placed in a queue, allowing workers who are available to pull the item with the highest priority that they’re qualified to perform. In contrast, work items are directly assigned, or pushed, to team members in a push system by a manager.
A lean organization uses cycle time and throughput as the key metrics for measuring flow in a pull system. Cycle time is the time that a team spends actively working on completing a task, whereas throughput is the number of tasks it completes within a given time period.
Leaders in a lean system will strive to reduce cycle times and increase throughput.
5. Seek perfection
Seeking perfection means that a team should constantly improve processes, generally by enhancing activities that generate value while eliminating those that don’t. This step uses a number of methods such as Plan, Do, Check, Act (PDCA), but it’s really more of a mindset that leaders need to instill in team members.
Continuous improvement requires all team members to embrace ownership of their processes, so leaders often need to place more trust in the expertise of their team members. Daily stand-up meetings are an effective way of keeping team members accountable, as it requires each member to explain what they did the previous day.
Benefits of implementing lean principles
The benefits of implementing lean principles include improved process efficiency, increased productivity, and reduced costs.
Better business processes efficiency
Improved efficiency is one of the most obvious benefits of lean principles. Based on the particular method you use to measure success, these improvements can manifest in various ways.
Lean management bases production on demand, meaning it only uses required resources, giving teams greater flexibility in handling dynamic changes in customer requirements. In addition, lean principles help create more stable production systems, leading to better chances of improving process performance.
Increased productivity
Lean principles increase productivity by minimizing waste like material defects, which can be corrected by adjusting a poorly maintained machine. Other types of waste are based on environmental conditions that impair worker productivity, including poor ergonomics.
These sources of waste can often be eliminated with simple solutions such as eliminating redundant work by automating notifications or alerts.
Reduced costs
Eliminating waste from processes can also reduce costs and increase daily profits. It also provides organizations with the opportunity to invest those profits in things that will help them grow, including employee training or additional resources.
Reading recommendation: A Simple Guide to Lean Process Improvement
Best practices to implement lean principles
Implementing lean principles requires three best practices, such as setting clear goals, developing a lean culture, and expanding slowly.
Define clear goals and KPIs
The leader of a lean initiative needs to know what its end goal is and communicate that goal to team members. This goal should be easy to understand, like optimizing the workflow to deliver products more quickly, increasing profit, or improving organizational agility.
Sharing the path to this goal will help remove obstacles in your way and motivate others to take this journey with you.
Develop a lean culture
A culture that embraces lean principles is essential for leading change, rather than simply managing it. Obtaining buy-in from stakeholders can be a challenge with lean, as it represents a major deviation from traditional manufacturing methodologies.
Begin this transition by explaining what lean is to team members, ensuring they understand its benefits from both a personal and organizational perspective. Be sure to also cover why a lean culture is necessary to eliminate waste and deliver better value to customers.
You also need to cultivate the concept of shared leadership, in which team members have greater responsibilities. Making these ideas clear will increase the probability that team members will adopt these practices.
Expand slowly
The transformation of an entire organization to a lean organization is usually a slow process. Managers typically implement lean principles in one team first, before doing so with teams in other departments.
For example, an enterprise will often form a cross-functional team to serve as a pilot group, allowing team members to serve as change agents when they return to their original teams.
A large research and development department can be a good choice for this approach, which frequently consists of multiple teams working independently. Select team members who are enthusiastic about adopting lean principles and influential within their original teams.
Get lean with Pipefy
Lean management principles continuously improve processes, helping organizations and their members achieve the best version of themselves. Pipefy’s no-code automation platform makes it easy to design and scale lean workflows. With real-time process tracking, keep track of bottlenecks, inefficiencies, or waste and quickly draw insights for data-driven optimizations.