ARTICLE SUMMARY
A Kanban board is a visual representation of the workflow and is divided into lanes filled with color-coded cards. These cards have relevant information for that particular part of the process. These can be physically represented by a whiteboard and post-it notes or digitally represented by software, just like Pipefy. So once Kanban is used to manage your tasks or processes, the next big choice you’ll face is what type of Kanban Board is ideal for your environment: physical or online.
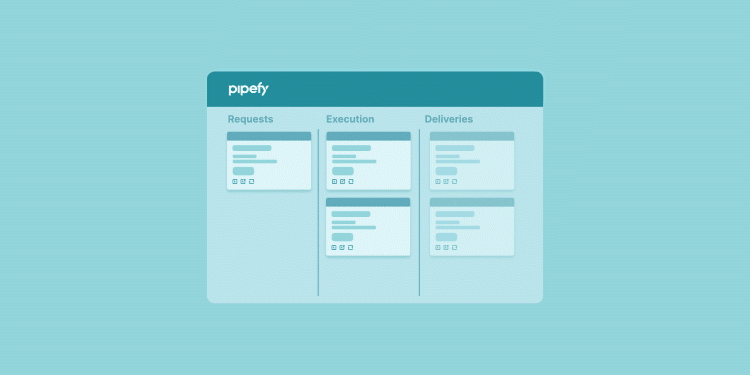
There are few tools as valuable in the business world as a Kanban board. With Kanban taking over the way most businesses manage their workflow, it’s important to know what is a Kanban board and how it works.
What is a Kanban Board?
A Kanban board is a visual representation of the workflow and is divided into lanes filled with color-coded cards. These cards have relevant information for that particular part of the process.
These can be physically represented by a whiteboard and post-it notes or digitally represented by application software, like Pipefy. So once you, your team or even your company decide using Kanban to manage your tasks, the next big choice you’ll face is what type of Kanban Board is ideal for your environment:
- Physical
- Online
Physical vs. Online Kanban Board
Although physical Kanban boards—the stereotypical boards with color-coded sticky notes—have been proving to be extremely effective at getting the job done and giving people the help they need to put task management in place, they don’t quite provide the versatility you may have expected when used offline or physically—at least, not in comparison with the online Kanban board.
An online Kanban board has the advantage of granting access much more easily to your general Kanban planning—for everyone to whom you wish to grant access to—, ensuring that your entire business can grow and develop with the changes.
There are many benefits in understanding the main differences between these two types of Kanban Boards, including making an informed decision and implementing the model that best suits your own business.
However biased it may seem, since Pipefy is, in fact, an online Kanban board tool, we have to recommend the online Kanban board due to all the reasons below:
Online Kanban Board
- Easy access to everyone, anytime, everywhere: an online Kanban board gives you an easy way to visualize the work processes that can be easily available to everyone, wherever they are
- The online Kanban board card structure is usually very self-explanatory, eliminating the necessity of explaining the goal and requirements of the current process in the overall task. This makes it easier for your staff to understand what is going on and to explain to external workers involved in the process in what part of the process you currently are
- Online Kanban boards allow you to easily limit the amount of work in progress in your processes (especially the ones that are being held up), as it can be hard to list this information clearly and openly on a physical board. With online boards, though, it can all be easily categorized and understood much more clearly than with physical boards
- Online Kanban Boards sends you warnings (via email) to notify people when the deadline of a task is coming or if it expired. This is very helpful, especially with time-sensitive tasks
- More importantly, though, the task is massively improved if it is easier to focus on the workflow—because everything can be seen online. Forget going to the office to get a project update!
Physical Kanban Board
- A physical Kanban Board can be very effective because it provides a central place from where everyone in your team can gather information to brainstorm
- However, it pales in comparison to the online Kanban board in terms of making sure that everyone can remain updated at all times—people have to physically go to the board to get the information they need, instead of getting online alerts of their due dates
- It also needs to be physically updated, whereas making online changes is much quicker and easier
- A physical board can be checked only during the opening hours of your workplace and it ceases to be the easy reference point it once was when the staff members who are being asked about the project by investors and others are away from the office
Taking the time you need to make the right choice for your business is very important. However, if you have the budget availability and if the technology alternatives are open to you, then an online Kanban board will definitely work best.
Learn how an online Kanban board works with Pipefy!
Just like its physical counterpart, an online Kanban is divided into vertical lines that represent the phases of the workflow. Kanban cards with your work tasks are moved through the lanes via drag and drop as progress is made.
The cards have visual icons that help you communicate important details, such as priority, issues, owners and estimated due dates. The different types of work in the process are symbolized with the use of different colors—or labels—for each one. It gives you a quick visual idea of in which point of the process the work is, what type of work is being done and what needs to be done next. This can be communicated worldwide and instantaneously, thereby increasing efficiency and reducing or even eliminating guesswork.
The innovation and communication available to users of online Kanban boards cannot be beaten, not even by their physical Kanban counterparts.