ARTICLE SUMMARY
To keep track of your tool and inventory with Pipefy, first we created two databases: one for the employees’ data and one for the equipment’s information. Then, we created a specific pipe to match these two pieces of information, so it’s easy to know who is using which equipment, with specific details.
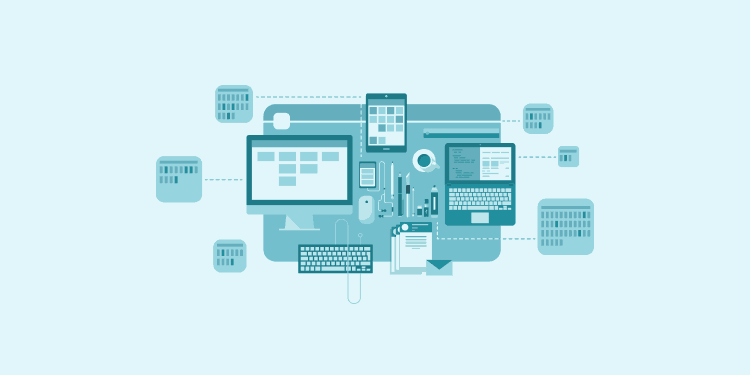
To perform any job, you’ll need the proper equipment, that most of the times is provided by the company. For example, here at Pipefy, with few exceptions, employees receive notebooks, mouses, monitors, keyboards, and headsets.
Keeping track of the tool and equipment inventory is not considered a crucial activity in a company, but the lack of control in this area can cost money and make your employees produce below their potential.
When your company is small, equipment inventory might not seem a big deal, right? This problem gets increasingly bigger and gets especially worrisome when it comes to fast-growing companies, such as startups that grow from 5 to 50 employees in a year.
We found the perfect way to deal with this matter with minimum effort and maximum reliability. If you want to learn to do the same using Pipefy, just keep reading!
Golden Tip: These Are the Real Assets for Any Startup
Why control your tool and equipment inventory?
- Your staff is the most precious asset of your company. Your physical assets (your tools and equipment) are also precious, though. Unless you’re an extremely lucky person that got all your equipment for free, it’s very likely that you’ve spent a fairly large amount of money purchasing equipment. To keep track of these items is to take care of your investments
- If you are in a tech company, like we are, it means that most of your employees spend 99% of their working hours in front of a computer. If they don’t have the right equipment, they will produce less—or nothing at all
- Each employee receives at least 3 or 4 pieces of equipment. As the team grows, it gets exponentially more difficult to keep track of everything without a dedicated process. Fortunately for us, we had all the tools we needed
How you can use Pipefy to keep track of your company’s tool and equipment inventory?
The only other thing we needed besides the Pipefy platform were barcode numbered labels (you’ll know why in a few paragraphs). You may use them or not according to your needs. We felt that they made it easier to quickly identify equipment without the necessity of reading long serial numbers.
The first thing you should do is create two databases:
- Employee database: A simple employee database with as many details as you deem necessary. If you’ve already created an employee database to use in another process, you can use it for this goal too
- Tool and equipment database: List all the equipment you have. Add relevant information such as type (computer, cable, mouse), brand, model, description, etc. We also added the number of the label and each equipment’s serial number
Once that was done, we’ve created an ‘inventory’ pipe with the following phases:
- Requests: equipment requests waiting to be fulfilled (they move to ‘in use’ after an employee’s formal acknowledgment)
- In use: equipment currently assigned to an employee
- Devolutions: equipment that was put back in stock for any reason (no longer necessary, the employee is no longer working at the company, etc.)
- Under repair: damaged equipment, undergoing repairs
- Obsolete: old, broken or lost equipment, no longer functional
The pipe’s start form must have the following fields:
- Employee data. A connection field linked to the employee database (make sure you choose “search database records” and “single entry” when creating the field)
- Item/equipment. A connection field linked to the tool and equipment database (make sure you choose “search database records” and “single entry” when creating the field)
- The date in which the equipment was taken from inventory. Date field.
How does it work?
If you understand how Pipefy’s databases and pipes work, you probably already see where I’m going. I’m always in favor of playing safe, though, so I’ll take my time explaining how the equipment inventory control process works, from the moment it starts when the equipment is requested until it’s ordered from the supplier, delivered and assigned to the employee.
Before the first step, an employee or a department requests new equipment, creating a new card on the purchase process pipe. The inventory process starts after the purchase is completed and the item is delivered.
Right after you check if everything was delivered according to what you ordered, you tag the new equipment and add new records in your tool and equipment database.
The next step is creating a card in your inventory pipe and formally assigning the equipment to the employee who will use it.
You can do that by asking them to reply to an email or by manually signing a term of commitment. Once they do it, you move the card to ‘in use.’ The equipment will be officially assigned.
You can easily keep track of what’s assigned to each employee by opening their employee database record.
Each related card will display the equipment that’s currently being used by an employee.
You can also work the other way around, accessing the equipment’s record to find out which employee is currently using it.
Use Pipefy to manage your equipment inventory since the first day of the employees
Pipefy is the Work Management platform that empowers doers to organize and control their work in a single place, enabling anyone to streamline and automate any business process on their own, resulting in outcomes of greater quality.
Pipefy can be used for many different things. With our easy-to-use IT Onboarding Template, you’ll always keep track of your inventory.